[tip_box]Definition 1: Waffle: To speak or write at length in a vague or trivial manner. As a child I was often accused of this. Come to think of it, I’m still being accused of this.
Definition 2: Waffle: A delicious dessert – a batter cake, like a pancake but crisper, baked in a waffle iron which gives it a grid-like surface. A Belgian delight and unfortunately one of my favourite deserts.
Definition 3: Waffle: In building a space saving device usually made of poly-styrene that is used in concrete slabs in order to limit the amount of concrete required to build a concrete slab. In my working life as a builder, something I try to avoid.[/tip_box]
Across Melbourne, particularly in housing estates built over the last twenty years, waffle slabs are common in homes built by new home builders, especially the volume builders.
Waffle slabs conform to the AS 2870 – the Australian Standard for Residential Slabs and Footings. But care needs to be taken in using them particularly on highly reactive clay sites, sloping sites, fill sites, or locations where drainage is a problem.
Melbourne’s Western suburbs, particularly the municipalities of Hume, Melton and Wyndham are located on a volcanic plain that runs all the way to Western Victoria. In fact, soils are volcanic (and therefore highly reactive) right through the western edges of Melbourne through to the Darebin Creek, which is the boundary between Northcote and Ivanhoe.
Waffle pod slabs have been linked to a phenomenon known as slab heave – where the slab lifts causing cracking and damage to the building frame. Windows cease to open and close, doors get stuck or won’t shut.
So what is a waffle slab? Sometimes referred to as a ‘waffle pod foundation‘ it’s a type of concrete slab used in house construction that uses poly-styrene spacers with a system of steel reinforcement between and on top of the styrene separated and held in place by small plastic supports known as chairs that keeps the steel mesh proud of the styrene.
On building sites around Melbourne the tell-tale sign that a waffle slab is about to be constructed would be pallet loads of large styrene cubes tied down on a building site, or set out ready for a pour. And they are tied down for a good reason as they are light as a feather and can be blown away by wind causing the cubes to break up into tiny pieces that are a nightmare to pick up and end up in our waterways.
When completed a waffle slab looks the same as the more traditional raft slab. Once the styrene and steel are covered with concrete all you see is the finished concrete.
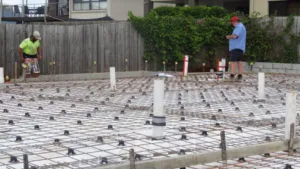
Waffle Slab laid out and ready for the concrete to be poured.
Waffle Pod Slab Cost
Promotors of waffle slabs put forward a case that this type of slab is cheaper, there are less site works required, hence less labour and contracting costs, and that there is better insulative properties through the ground to the floor of the house. There is also less actual concrete.
And these things are true, and particularly for the new home market where cost is an imperative, waffle slabs do cost less to construct.
When plans are drawn for any building prior to construction, there needs to be an assessment of the engineering requirements by a suitably qualified structural engineer. The engineer in assessing the slab requirements will look at the load that the slab needs to cater for in terms of weight from the structure to be placed on the slab (dead loads) as well as the potential additional weight from occupancy of the house (live loads).
So in this engineering context, what is a load? A load is a weight or source of pressure onto a structure. That pressure can cause stress and deformations in the structure if left untreated. It can come from many things, but they all work on a structure ultimately to return that structure back to dust (just like us) over a long period of time.
As a simple example think of external paint on a wooden window – if the paint is chipped or weathered from the action (or loads) of sun and rain over time, that protective coating if it fails can then cause damage to the underlying structure, in this case the window. Eventually the window will rot and need replacement. If left untreated it will start to affect other parts of the structure.
Loads can come from actions applied to a structure and can include weight, sun, wind, salt, fire, water, mould, earthquakes and accidents. Buildings need to be designed to respond to these loads so that they remain safe and habitable for the occupants.
Any expected loads on a building need to be met with an equal force that will keep that load at bay and therefore keep the structure sound. Maintenance is also essential.
In any engineering assessment, there is a requirement that construction addresses at least the minimum expected load on the slab. If the slab is built to a minimum (rather than better than the minimum) requirement there will be a resultant cost saving.
However, after construction is completed, if the owner of the house wants to do a second storey extension or renovation to the house, having a slab that only addresses the minimum engineering standards to the existing house is not helpful in making modifications to the existing structure.
When designing a second storey extension consideration needs to be given to the existing foundations. The home extension needs to be designed in such a way that the various loads are catered for adequately and does not deteriorate or fail. The weight of the upper storey structure needs to be transferred down to the foundations, which need to offer sufficient support. If they do not offer that support the second storey extension would ultimately fail.
When Supa Group are adding a second storey addition to a house that is built on stumps, the engineering may require additional stumps to be added to the existing home as load bearing stumps. The building load from the upper storey is transferred down through to those points via steel beams inserted into the walls of the existing house.
[service_links]Get inspired by browsing our range of extension projects.[/service_links]
So the issue with extending a house with a waffle slab is that, in most cases, the slab is not designed to take any more load than what is already there. In order to add a second storey extension, modifications to the existing slab may be required and this may mean cutting away the existing slab and replacing that part of the slab with a structure that can take the load. But cutting existing slabs can create other problems, so it’s really a last resort.
As for ground floor extensions, if the existing house is a waffle slab, that in itself is not a problem as you can construct the foundations of the ground floor extension with any type of footing appropriate. However in the new housing estates, block sizes are generally smaller and the issue of site coverage becomes a planning issue. Site coverage limits are designed so that room is left for outside open space. Adding ground floor extensions in this scenario may not be possible as that will increase the site coverage beyond what is allowed.
If a slab is required, at Supa Group we do not build with waffle slabs, instead using the more traditional raft slabs.
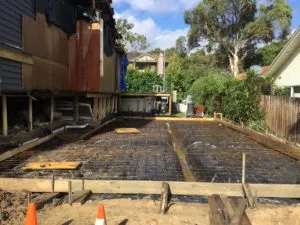
A raft slab laid out ready for the final pour.
A raft slab is a reinforced concrete slab with strip footings and edge beams surrounded by formwork. The first step to constructing the edge beams is to create the footings for the edge beams which are poured before the actual slab is formed. Steel bars are placed into the concrete for the top of the slab to attach to.
The slab is then laid out using sand to get the slab to the correct height. Channels are formed for the strip footings and edge beams. The sand is covered with black plastic sheet and on top of that the steel mesh is laid sitting on a series of chairs. The mesh gives the slab its strength.
The benefit of a raft slab is that it firmly attaches to the earth. The engineering report for the slab will determine the depth of the edge beams. This is determined by the soil type and whether there has been any fill on the site. If the site is an old fill site the engineer may instead prescribe screw piles instead of the edge beams.
While waffle pod slabs are problematic, there are instances where alternative solutions can be designed. You should contact us to discuss your individual circumstances, but first try to find the plans for your house, especially the engineering drawings as they will be a great help in any assessment.
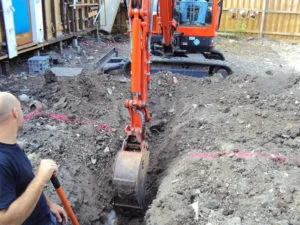
Digging the footings
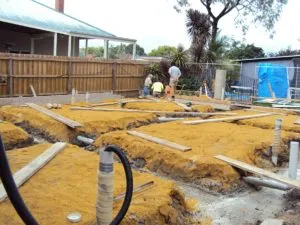
Sand laid out ready for tarping. Services are already installed and ready.
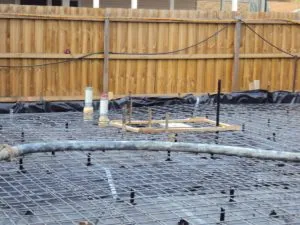
Tarped and steel reinforcement in place
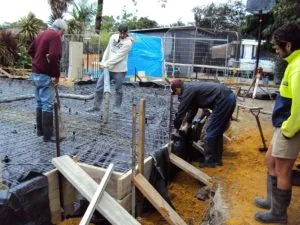
Pouring the slab
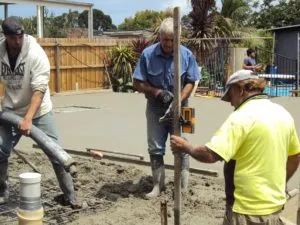
Checking Levels
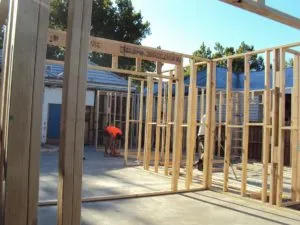
Completed slab with framing commenced.
[free_consultation]Get in touch today to find out how we can help with your renovation or extension.
[/free_consultation]